Digital twin technology is one of today’s brightest and most useful innovations for solving key business challenges across a wide range of industries.
Digital twins are no longer a futuristic technology, but a reality for many companies. How does the technology work and what can you model with it? What are the benefits of digital twins and how are different industries using them?
Find answers to these questions and more in this article.
According to our Digital Twin Market Report 2023–2027, the digital twin market is expanding, with a projected CAGR of 30% between 2023 and 2027.
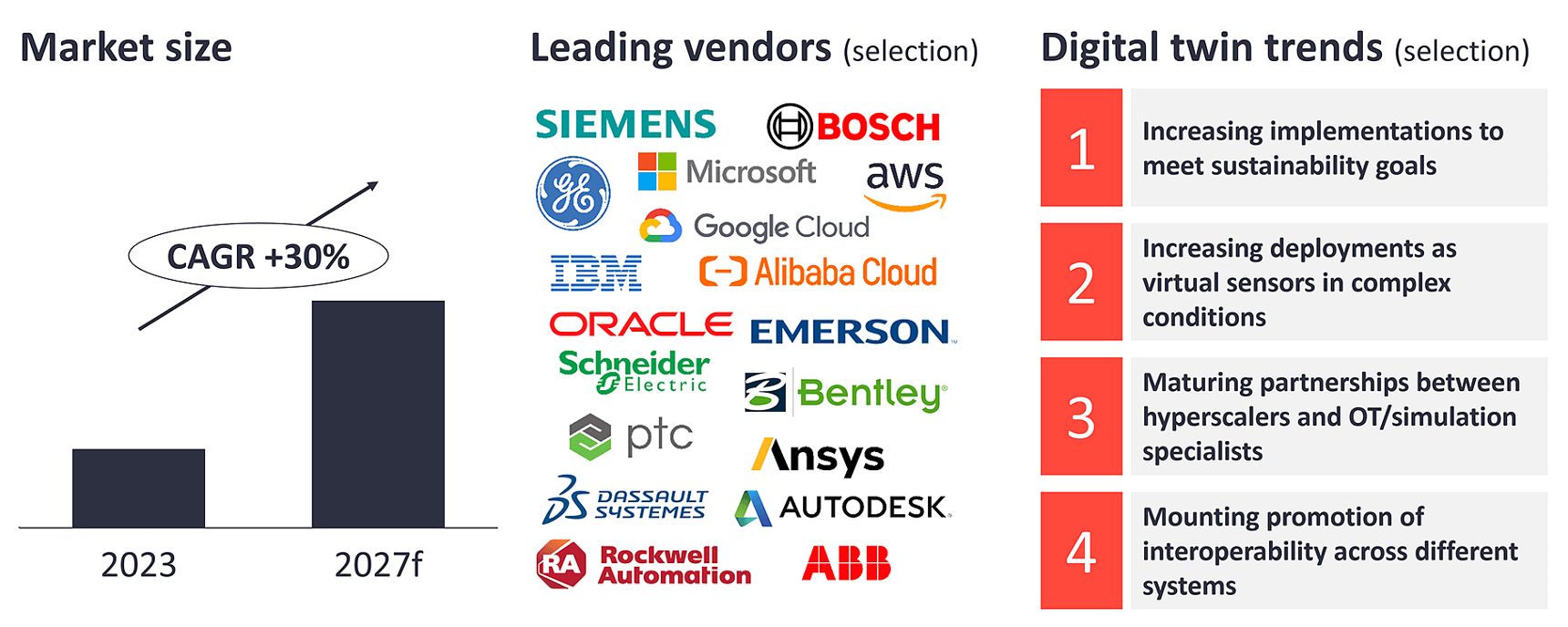
What is a Digital Twin, and How Does this Technology Work?
A Digital Twin is a virtual interactive copy created based on a real object or process, duplicates it in its key features, and can reproduce its state under different circumstances.
For instance, a factory digital twin helps the management monitor work processes, check equipment status, build process behavior forecasts, and prevent emergencies. In fact, it is a kind of “bridge” between the digital environment and the physical world.
Nowadays, the digital twin technology has successfully found its way into the automotive, urban planning, and aviation industries. It also ensures people’s safety when working in harsh and hazardous environments.
Comprehend the difference between a digital twin and a digital model. The former finds its use mainly in production and serves to “describe” a specific node or unit, so its task is more specific. The latter can carry out more general tasks.
Sensors on the real-life device collect data about its operation parameters and transmit them to its computer simulation that imitates the target object’s features and ongoing processes. A digital twin may appear earlier than its real-life counterpart: manufacturers develop it to test equipment operation and identify possible issues long before a physical device comes to a production line.
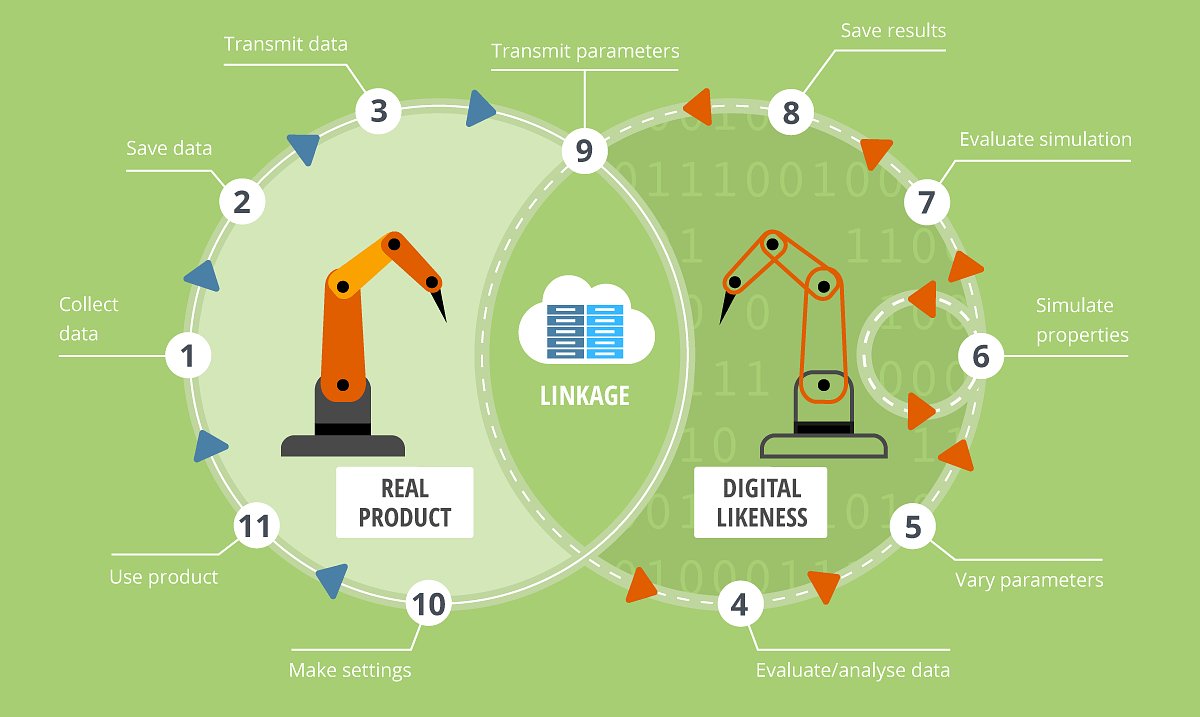
Three stages are necessary to implement a digital twin.
- A system comprising numerous sensors placed on a real-life object evaluates the necessary parameters as exhaustively as possible at any specific instant.
- An exact digital copy of this object is reproduced in the virtual environment.
- The object’s physical sensors transmit a continuous data flow to its digital counterpart. The goal is to simulate the current state of the object in a simulated environment.
Experts can digitally prototype almost any object, starting with a single piece of industrial equipment and finishing with an entire production plant. IoT, AR/VR (for visualization), and Artificial Intelligence are the primary technologies used for simulations.
Looking for Digital Twin development services?
We specialize in VR/AR digital twin development, data analytics and IoT development. Build a digital twin with a trusted tech partner.
Get in touchCommon Types of Digital Twins
Conventionally, we can divide digital twins into several types depending on the scale, application vector, and operational peculiarities:
Product/Mechanism Digital Twin
Companies can simulate the load applied to products, evaluate their durability, and test possible damage tolerance. This approach allows production companies to shorten the design cycle, reduce its cost, and bring the product to the market faster. As a result, the projected product becomes cheaper and ensures higher profits and competitive advantages for the production company.
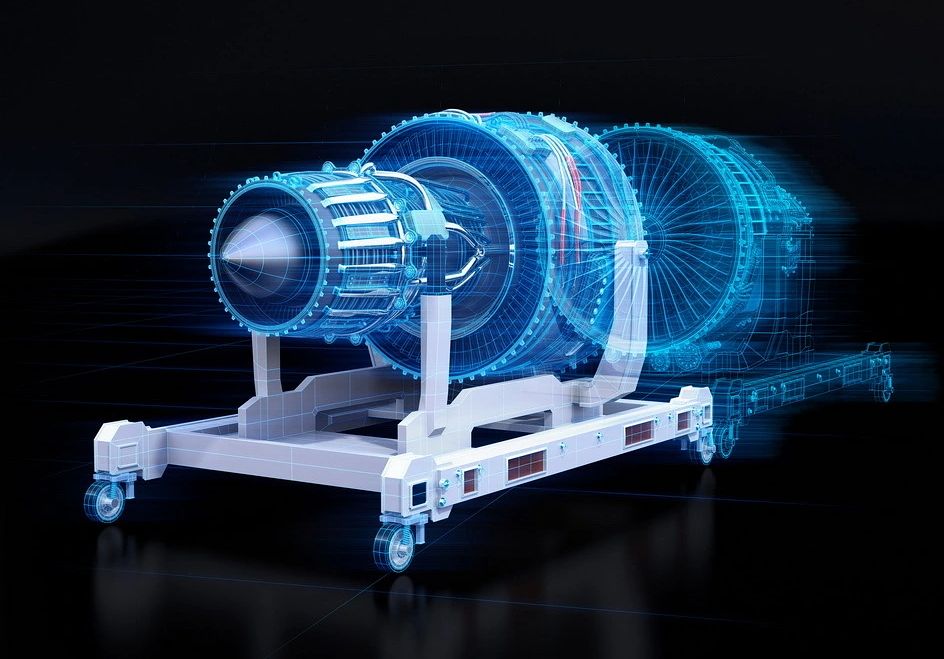
Technological Process Digital Twin
Production companies can also improve their production process by using digital twins. Specialists can find optimal production process parameters, enhance product quality, and reduce energy and resource consumption during the production process.
System or Unit twins
System or unit twins are the next level. They allow specialists to see and evaluate how different assets combine into a single operating system. For example, the ones interested can create a digital twin simulating an entire plant.
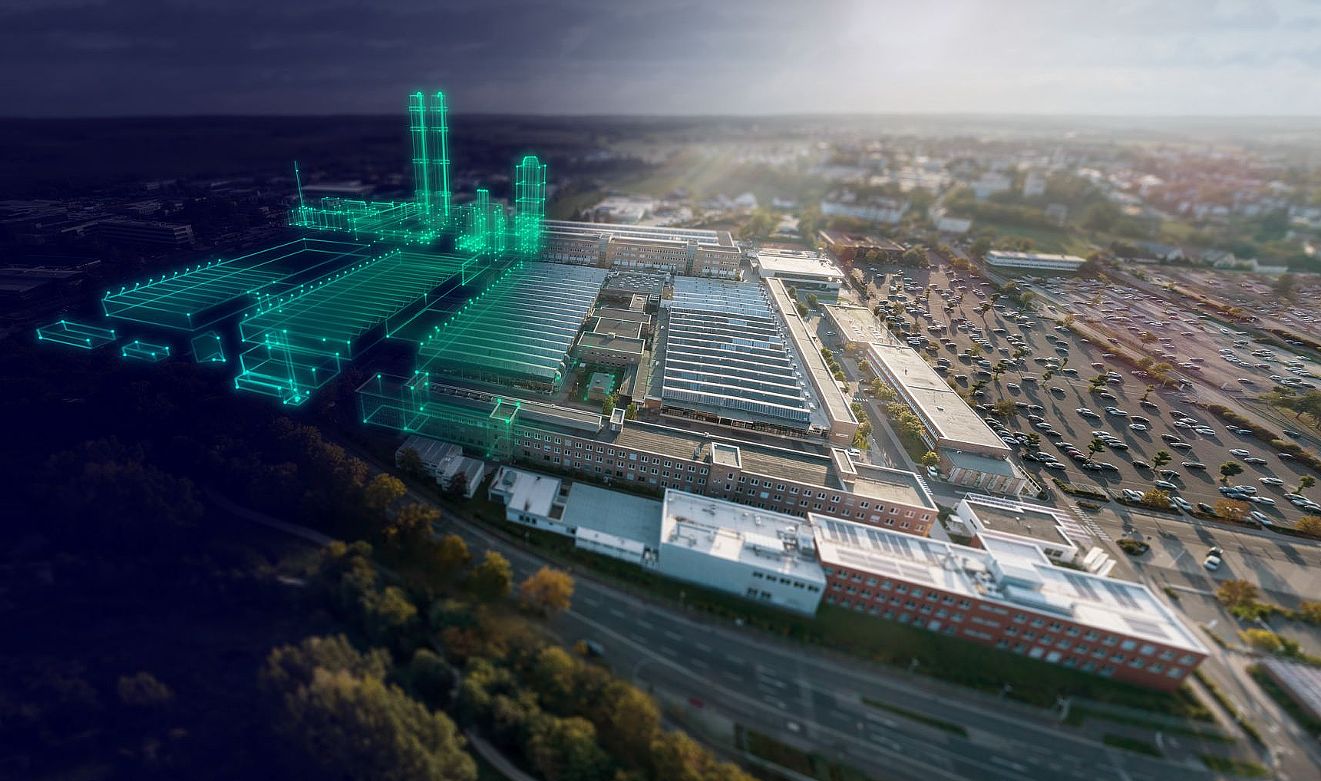
Based on the model that takes into account a relatively large number of parameters and restrictions, companies can reduce production costs, optimize limited resource consumption, and shorten the production cycle.
Digital Twin Aggregate (DTA)
It is a system that combines all digital twins and their real-life prototypes and enables real-time data collection and exchange.
The Benefits of Digital Twin Technology
Here are some benefits the technology provides when practically applied:
- Increased system efficiency and reliability. A digital twin will help companies design any system and its elements to achieve the maximum efficiency possible from using it.
- Reduced reaction time to emergency. Due to real-time situational monitoring and predictive accuracy, a digital twin can minimize response time to a breakdown, accident, or other similar situations.
- Simplified planning and decision-making. Detailed data received from digital simulation monitoring systems allows experts to consider numerous factors and likely scenarios, create quality instructions, and make data-driven decisions.
- Cheaper complex experiments. Physical object reproduction can be a complex and expensive task. In this case, a computer model replaces it and simulates its condition and environment. Consequently, the created computer model is subjected to experiments aimed at finding successful solutions. Another example describes a situation when specialists must test a hard-to-reach mechanism or measure difficult-to-track process parameters. Companies operating in any industry can conduct such experiments, be it manufacturing, metallurgy, oil production, or others.
- Lower maintenance costs. This effect is achieved by predicting possible failures before they actually occur. Thus, the approach goes from reactive to proactive, and planned maintenance and repair work does not affect production objectives.
- Better R&D. When applied, digital twins allow companies to obtain a massive amount of data about probable work results under specific conditions. This approach makes product development and various research more efficient. So, a company can gain important insights and make valuable improvements to its product before production begins.
In advanced industries, survey data indicate that almost 75 percent of companies have already adopted digital-twin technologies that have achieved at least medium levels of complexity.
— McKinsey & Company
Transform your data into valuable insights
We specialize in developing data-driven digital twin software. Our software is designed to accurately replicate your machines, workflows, and infrastructure.
Get in touchChallenges and Difficulties in Implementing Digital Twins
As is the case with any other technology, digital twins face inevitable challenges.
- High start-up costs. Dedicated hardware and software require financial investments at the start of implementation. Once companies have no staff qualified to conduct this task, they must look for experienced contractors.
- Integration difficulties. Digital twin complex integration with an actual building, mechanism, or process is complicated and requires financial resources and time.
- Qualified experts. To manage digital twins, employees should acquire expertise that will allow them to develop, maintain, and upgrade such a high-tech system.
- Privacy and data storage. It is vital to organize reliable storage of data delivered from sensors to a digital simulation system and processed by it.
Dedicated specialists should mind these difficulties when planning digital simulation system implementation. Not every company has sufficient internal resources for this endeavor. Consequently, it often makes sense to transfer this task to a third-party company that deals with relevant technological solutions. Then, when the technology becomes operational, a company can focus on the practical application of the resulting product.
Digital Twin Applications and Use Cases in Different Industries / by Industries
The list of industries where this technological solution can be utilized to benefit companies operating in them expands each year. Let us have a look at some of them.
Manufacturing
On the manufacturing floor, digital twins can collect data from various machines and equipment installed on the production line. This approach allows specialists to identify bottlenecks, predict malfunctions, and increase efficiency.
The manufacturing segment accounted for 26% of the digital twin market share in 2023, propelled by the growing need to create virtual replicas of their production processes, equipment, and supply chain operations.
— Global Market Insights
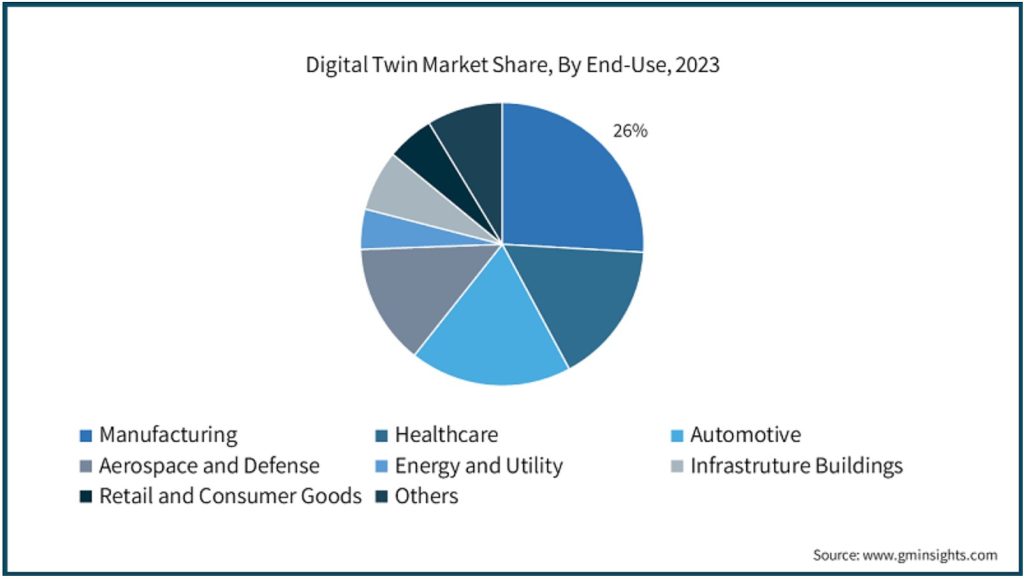
Oil and gas industry
Here is an example of digital twin use: “smart” oil or gas production wells equipped with all kinds of sensors that transmit data to the system and inform it about everything happening at the extraction point.
Based on this information, algorithms make decisions to adjust processes, select the drilling mode, notify of necessary repairs or equipment replacement, and notify of potential malfunctions.
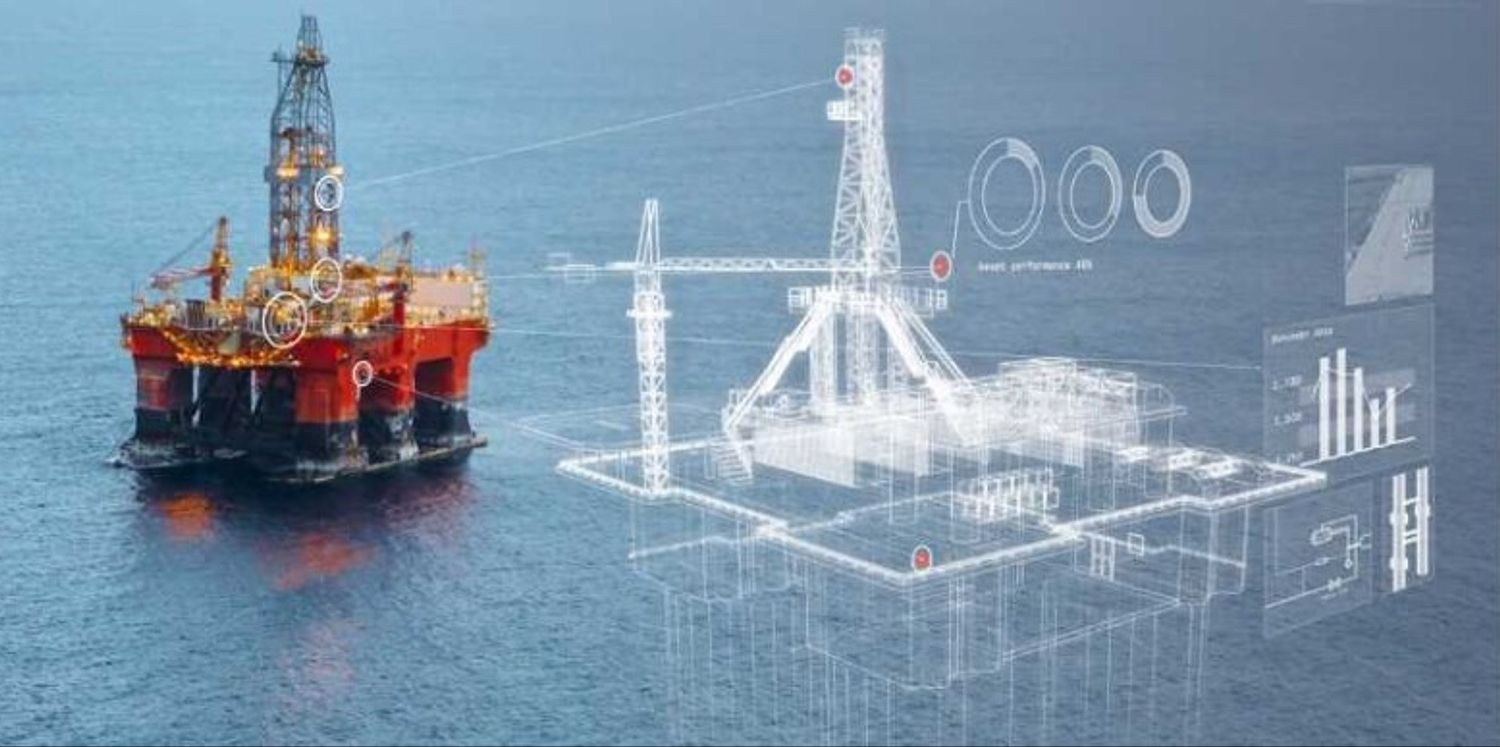
Metal and mining industry
Virtual prototypes allow mining companies to enter data about a resource deposit and all the features peculiar to the mining process into the system in advance. Using this data, experts determine locations to extract ore, what amounts to extract, and how to organize the process efficiently.
In the chemical industry, such emulation helps companies test complex chemical processes beforehand, taking into account raw mineral quality and technological parameters.
Let’s drive innovation in your company!
Share your business needs and we will help you develop the perfect-fit tech solution for your organization.
Contact usAutomobile and aircraft engineering
In aircraft construction, a digital twin simulating an engine allows experts to virtually test its operation under various loads, temperatures, and critical conditions. For instance, testers can simulate the situation of a bird getting into a plain engine and figure out how to prevent machine destruction in real-case scenarios.
Virtual models representing car parts allow companies to test them before production and save costs significantly.

Logistics and transport
In this regard, specialists can replicate all elements incorporated in multi-level supply chains and thus simulate various situations. That is crucial for large transportation companies because such businesses will eventually experience increased supply chain costs due to delivery volume growth.
Power industry
Experts in this field can create a digital twin of an entire wind farm. Then, using a computer model, they can choose the optimal operating parameters for each wind generator, taking into account factors like the geographical location and even the season.
Healthcare
Healthcare professionals can use digital twin technology to practice and mitigate risks during surgeries. A virtual system can simulate the flow of people through hospitals and track where infections can “penetrate” and who might be at contamination risk.
Health experts can use virtual simulations to develop new medical devices and analyze drug effects on the human body.
Urban planning
Digital twins allow respective professionals to develop urban planning solutions, manage the urban economy efficiently, and forecast the needs of newly-developed territories. We can distinguish several key directions here: infrastructure simulation, transport network, city ecology, and other processes.
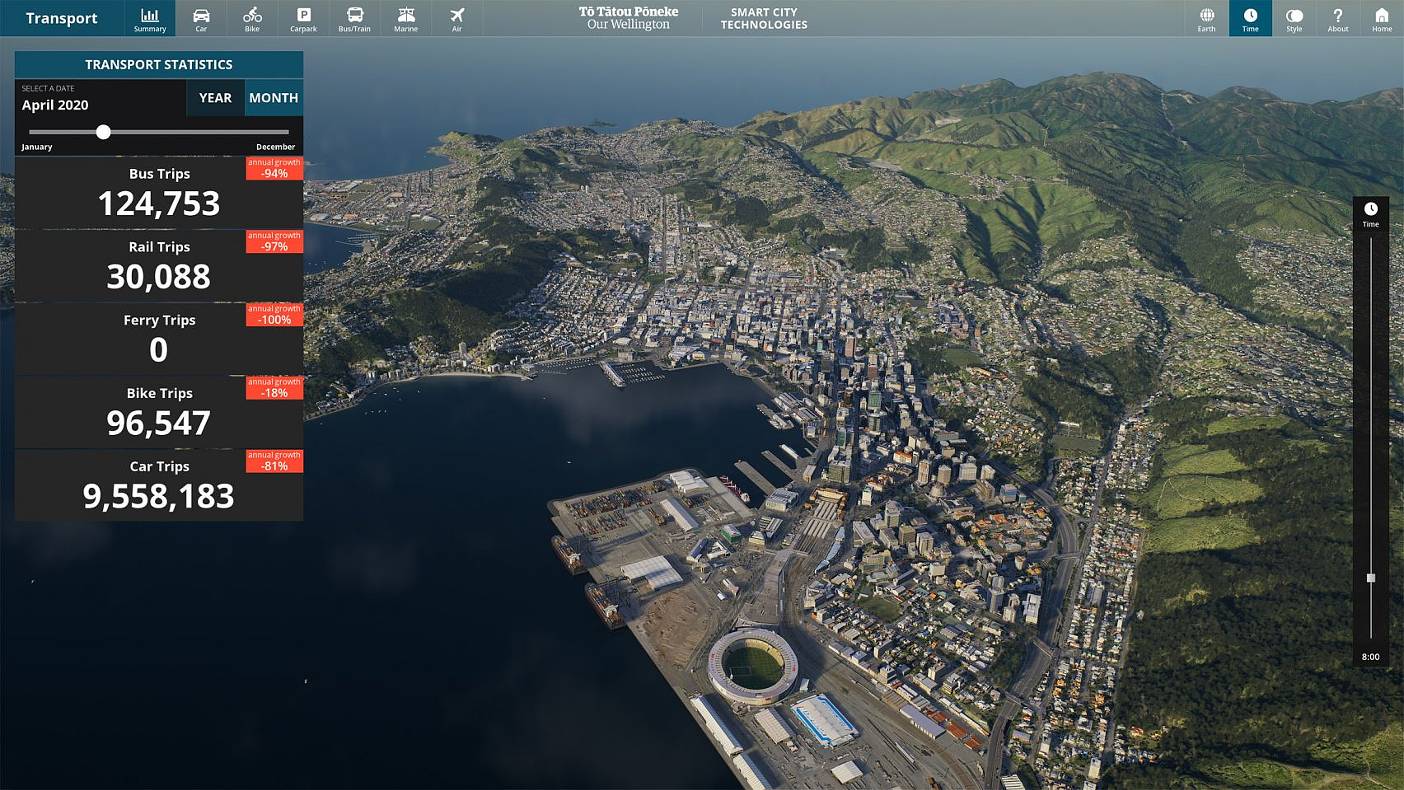
Harness the Power of Technology in Your Business
In every industry, digital twins have their own scope, use particular approaches, and resort to specific algorithms and development technologies. They help businesses solve multiple meaningful tasks and make correct management decisions.
Implemented digital twins can provide businesses with adequate returns that far exceed the expenses entailed by their creation and maintenance. Such solutions ensure numerous advantages and can help you fully unlock your company’s potential.
Get in touch with us to learn more about the applications of digital twin technology and how we can help you implement it.